Windows of opportunity: leveraging natural ventilation to create healthy, low carbon workplaces
The Future of Infrastructure
The way we design our buildings need to change post pandemic as we look to reduce operational carbon emissions. Smart buildings that use sensors and operable windows alongside mechanical ventilation systems can be both energy efficient and safe. Time to consider a combined approach, says sustainability expert Nathan Shelley.
The global climate and ecological crises have compelled the construction industry to take a new approach to designing, constructing and operating buildings in order to make them net zero carbon, resilient and truly sustainable. However, coronavirus has ushered in new concerns. We now need to optimise our buildings not just for net zero carbon, but for health too. To meet these challenges, we should re-examine traditional attitudes and approaches to ventilation and reconsider the carbon and business case for operable windows.
Modern offices typically have sealed façades and large amounts of glazing, requiring significant mechanical ventilation and cooling to maintain comfortable conditions for occupants and significantly increasing energy demand. In the wake of coronavirus however, designers and engineers are faced with a new dilemma – how to balance the need to reduce operational carbon emissions with revised mechanical ventilation protocols. As we build flexibility in our workplaces to switch between ‘new normal’ and ‘social-distancing’ modes, can these new ‘safe’ workplace strategies co-exist with our future net zero carbon ambitions?
In order to minimise the risk of coronavirus transmission, current British Council for Offices (BCO) guidance recommends that mechanical ventilation systems are run at full capacity and for longer durations to provide as much fresh air as possible. Currently, occupancy levels are being reduced by 50 per cent or more in many workplaces to allow for social distancing. At the same time, mechanical ventilation systems are running at increased capacity and durations. Therefore, the energy used per occupant is almost doubled. Meanwhile, home-workers will be using electricity and gas to run their home offices. The result is an overall net increase in company-wide carbon emissions.
BCO guidance also recommends that systems are run on full fresh air rather than recirculated air, which many systems are not designed forBCO: Thoughts on Office Design After Covid-19
. Recirculating air should be avoided but when it can’t, high-grade filters (i.e. MERV 13 plus or HEPA) are recommended to filter potential contaminated droplets and particles. While it is technically possible to retrofit these filters, it can be expensive while increasing the energy demand of ventilation systems.
So, what are the answers? We can enhance ventilation by designing mechanical systems to provide more fresh air into the workplace. Or, we can find a solution to improve ventilation that is still compatible with a future stable climate and ecosphere – smart operable windows.
The benefits of operable windows
The spread of coronavirus within occupied spaces is partly attributed to short-distance transmission via droplets (i.e. from exhalation, speech, coughing, sneezing) and suspended dust particles. Operable windows have benefits for mitigating coronavirus transmission, either to provide full ‘natural ventilation’, or to supplement mechanical ventilation, increasing fresh air rates and ‘flushing-out’ spaces between periods of use by different individuals or groups.
Current BCO guidance recommends that operable windows are kept open as often as possible and prioritised over maintaining thermal comfort for building occupants. Although intended as a short-term recommendation during the coronavirus pandemic, a variant of this approach has been around for many years and is known as the ‘adaptive building model’. An adaptive building allows temperatures to drift down in winter and up in summer, as opposed to typical modern offices which are air-conditioned and maintain relatively constant temperatures all year round. Company policies such as flexible dress codes and working patterns (potentially working from home on the hottest and coldest days) are essential to the success of this approach. For example, in Japan, the government runs the CoolBiz campaign every summer, encouraging office workers to dress comfortably and casually, to reduce electricity consumption for cooling officesJapan Today: CoolBiz campaign begins across Japan
.
Operable windows used at the right times can significantly reduce electricity consumption for HVAC systems. In the UK, exemplary buildings with low operational carbon emissions such as the Institute of Physics HQ in King’s Cross, London and GSK’s Centre for Sustainable Chemistry in Nottingham (both AECOM projects) use both operable windows and mechanical ventilation systems to ventilate the buildings in the most efficient manner depending on external conditions.
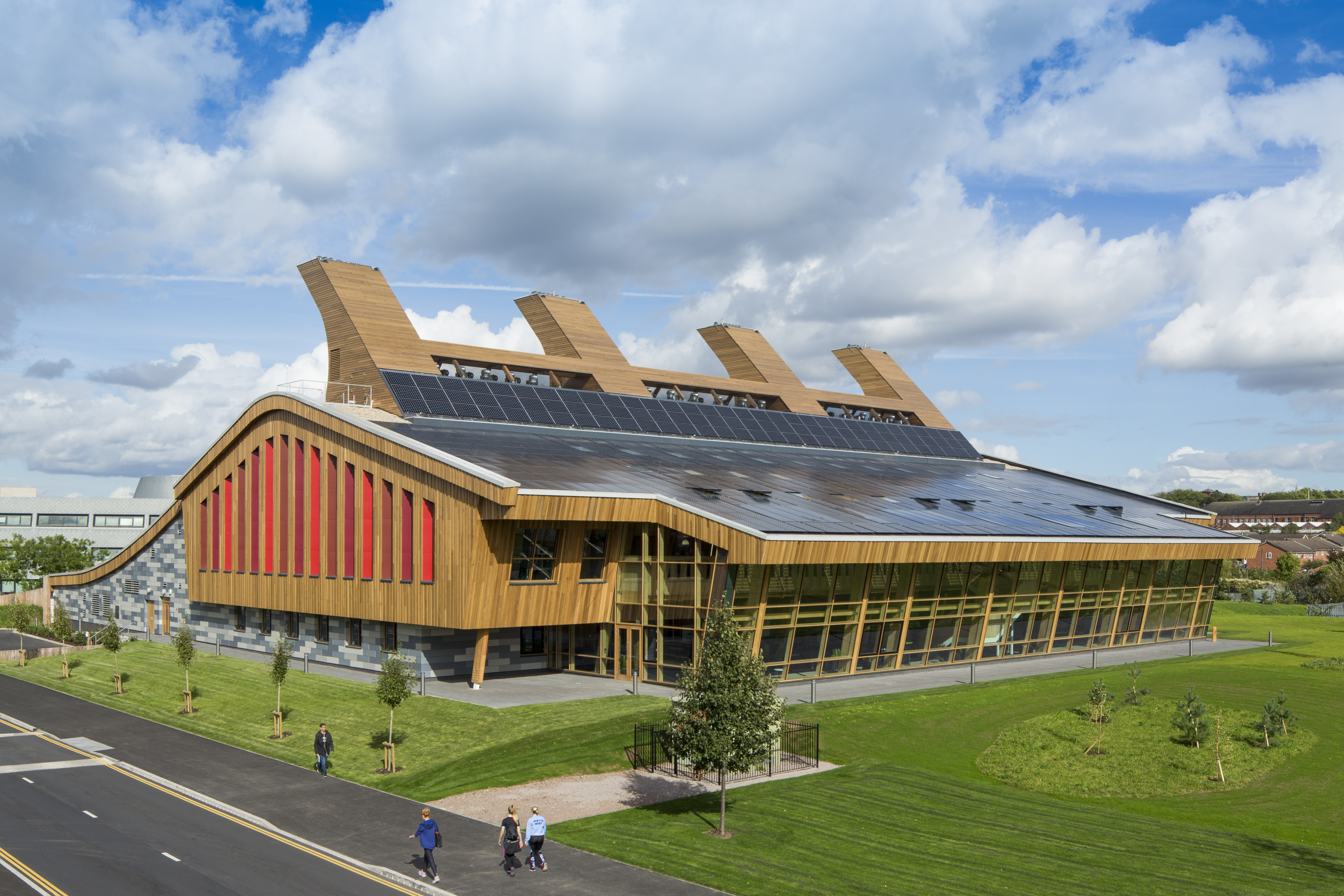
GSK's Centre for Sustainable Chemistry, Nottingham, UK
The method of controlling windows (occupant or automated control) has a significant impact on energy consumption. A fully-automated approach uses actuators (electric motor-driven automated window openers) linked to environmental sensors to automatically open windows. This approach has been taken successfully in buildings such as the NASA Sustainability Base in California, America. A well-implemented, fully-automated approach is optimised to reduce energy demand as it removes from the control process the unpredictability and potential for errors from human behaviour. However, it is complex – significantly increasing capital costs, maintenance requirements and negates any localised control for occupants.
If windows are manually operated, it is highly beneficial to include indicator display lights to inform occupants of the optimum times to open windows. This type of strategy is used successfully in the White Collar Factory office building in London. Windows are linked to environmental sensors, which may detect a range of environmental parameters i.e. internal temperature, CO2, external air pollution or noise levels. The use of sensors and indicator lights helps deliver energy savings, whilst having added benefits for occupant wellbeing, simplifying the systems associated with window controls and being much cheaper than a fully automated strategy. It is essential that staff understand how and when to use operable windows and that company policies are aligned to this approach, for example with flexible dress codes.
It is possible that future conditions will favour natural and mixed-mode ventilation even more and this is a key reason that forward-thinking developers are now considering the business case for operable windows. In terms of resilience and adaptability, operable windows allow for greater flexibility for future uses i.e. a future reconfiguration from office to residential or hotel would be better suited with operable windows.
With naturally ventilated buildings we also have an opportunity to significantly reduce the complexity, cost and maintenance requirements of mechanical plant. When controlled by occupants, operable windows also bring considerable benefits to wellbeing and productivity in workplaces, a particular focus of the White Collar Factory.
The way we travel in UK cities is also changing. Pollution in Central London has significantly decreased since the coronavirus lockdown began in April 2020. Although pollution may bounce back, the UK Government recently demonstrated a significant change in policy and funding towards promoting cycling, walking, electric scooters and electric vehicles and adapting Central London streets to discourage car use and prevent an increase in pollution to pre-coronavirus levelsGov UK: £2 billion package for cycling and walking
. If these policies are successful, there would be positive benefits for both air quality and vehicle noise, two of the often-cited barriers to the success of operable windows in commercial buildings.
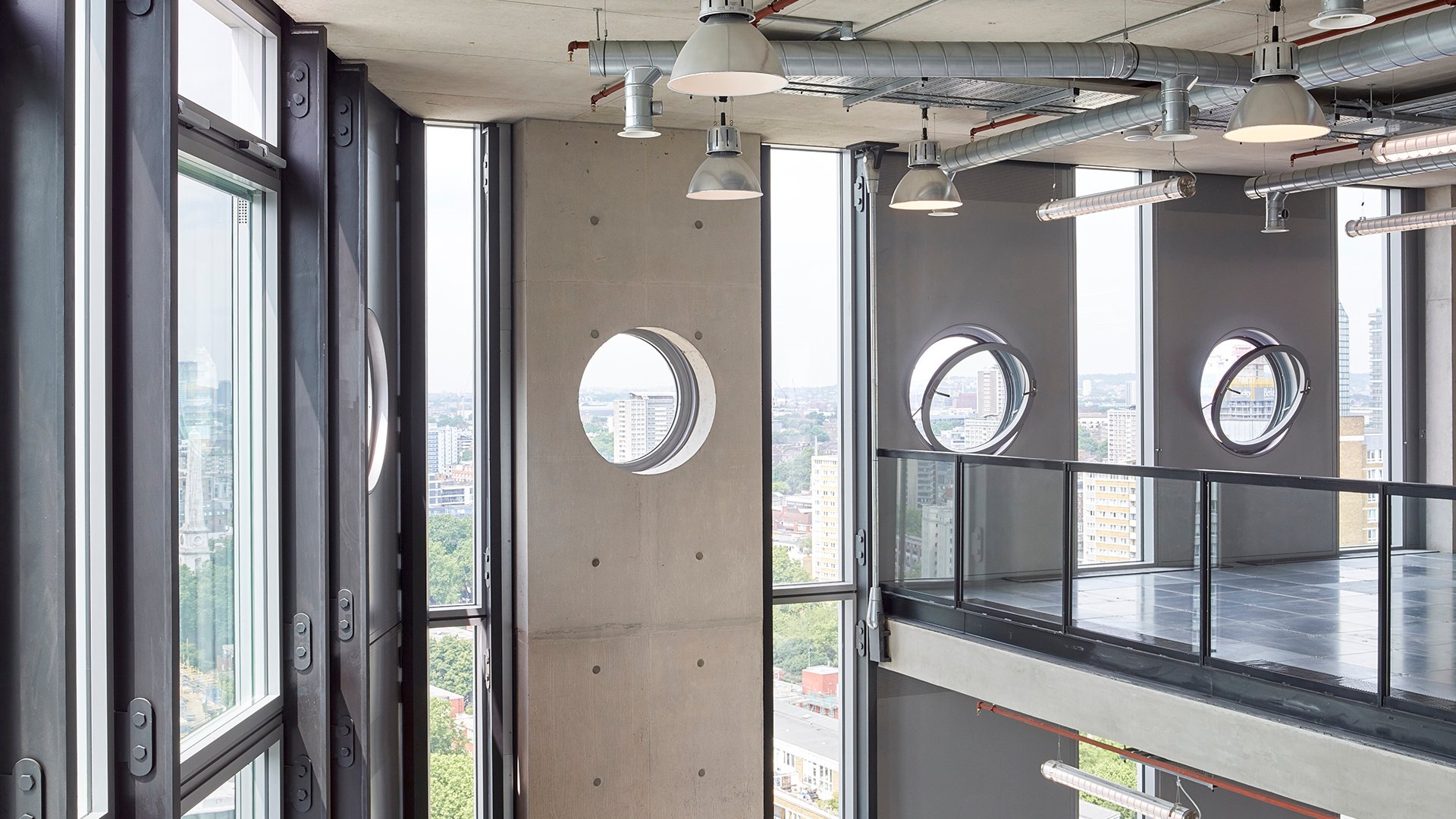
White Collar Factory (London, UK) uses two-metre high inward opening windows on office floors and porthole windows on the top two floors. Windows are controlled by occupants with a simple traffic light indicator system to promote energy conservation behaviour. When the system indicates conditions are suitable, windows can be opened with mechanical HVAC systems automatically switching off, saving energy (Photograph credit: Tim Soar)
THe time to rethink building design is now
We have a pressing need for a new blueprint of low energy and healthy buildings. In many aspects of commercial building design we face significant challenges in the compatibility of the two concepts. However, operable windows provide a viable solution which is tried and tested. Natural ventilation can improve health and wellbeing, mitigate the transmission of coronavirus, reduce energy use and operational carbon emissions. The way we design and use commercial buildings would need a rethink, but what better time than now?